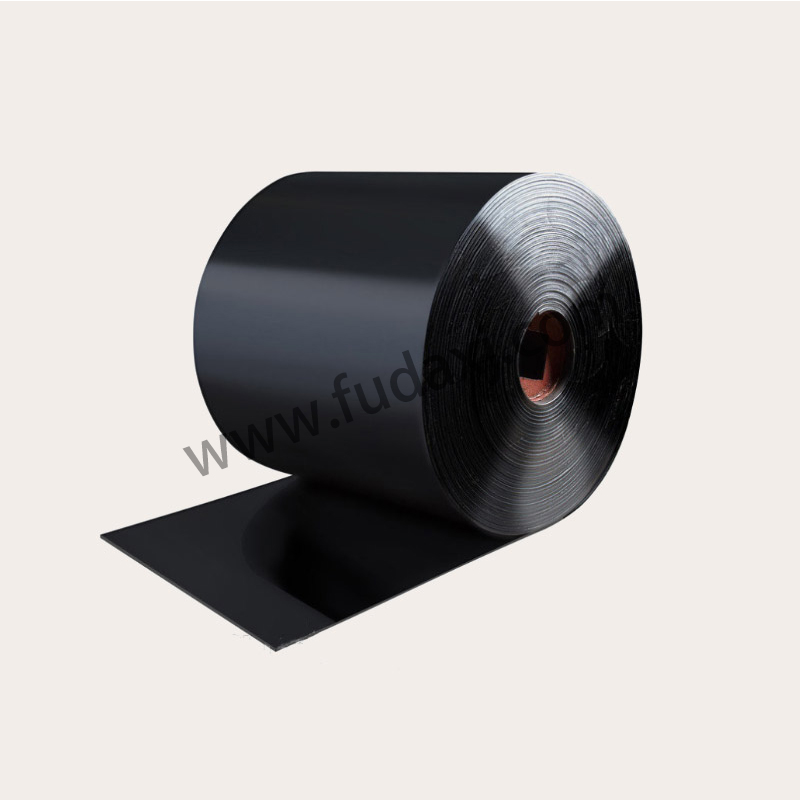
Characteristics of several conveyor belt materials
The rubber materials used in various parts of ordinary conveyor belts include cover rubber, buffer rubber, cloth layer rubbing glue, and cloth layer glue.
1. Cover glue
During use, it is subject to impact, abrasion and microbial erosion of materials, as well as various aging effects. Therefore, the covering glue is required to have good tensile strength (≥18Mpa) and wear resistance (abrasion amount ≤0.8cm3/1.61Km), aging resistance and biological erosion resistance. In addition, it is also required to have good technical properties such as viscosity. The main points of formula design are as follows: The raw rubber of the rubber technology network is mainly natural rubber or an appropriate amount of styrene-butadiene rubber is used in combination.
2. Buffer glue
The buffer glue is between the cover glue and the core layer, which can increase the adhesion between the two, absorb and disperse the impact force of the conveyed material, and play a buffering role. The adhesive is required to have good adhesion (adhesion between adhesive and cloth ≥3.15N/mm), high elasticity, low heat generation, good heat dissipation and good process performance.
3, wipe glue
The main function of rubbing glue is to bond the cored canvas layer into a whole. It is required to have good adhesion to the core material (the adhesion strength between the cloth and the cloth is not less than 4.5N/mm), fatigue resistance (the number of flexures of the cloth layer is ≥25,000 times/full peeling), and there must be enough Plasticity (plasticity 0.5~0.6) and process properties such as scorch resistance.
4. The raw rubber is mainly natural rubber, and 20~30 parts by mass of styrene-butadiene rubber is used, and the rubber content is about 50%. The vulcanization system is the same as the general sulfur and accelerator system. The accelerator is generally used together with M and DM, or a small amount of TMTD is added to speed up the vulcanization speed, but care should be taken to prevent the rubber from scorching. Carbon black should be semi-reinforced carbon black or other soft carbon black, and the dosage is about 10 parts by mass. The amount of coumarone resin and petroleum resin should be appropriately increased for rubbing glue mixed with styrene-butadiene rubber, otherwise the adhesion of the cloth layer will be reduced.