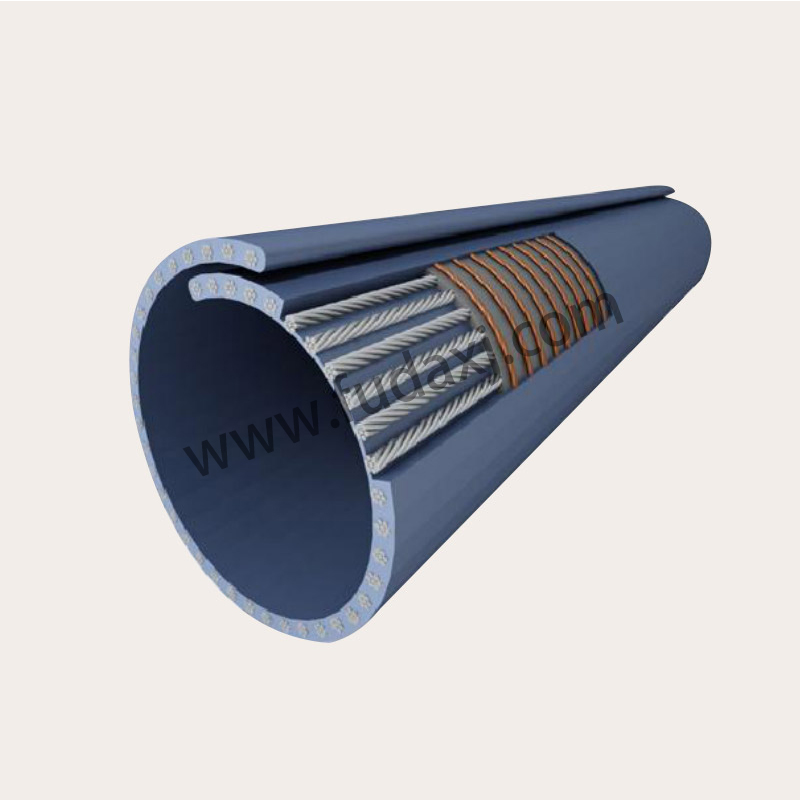
Steel cord conveyor belts are a significant component in large-scale bulk material handling systems. Unlike fabric-reinforced belts, steel cord belts are designed to accommodate higher load capacities and longer conveying distances. Beyond their mechanical strength, their manufacturing process and adaptability to diverse environmental conditions make them suitable for complex operational demands.
The production of a steel cord conveyor belt involves several coordinated steps that ensure structural consistency and operational reliability.
Cable Preparation: The process begins with the production of steel cords, which consist of several strands of high-tensile wire twisted into a compact form. These wires undergo surface treatments such as zinc coating to enhance corrosion resistance.
Cord Placement: The steel cords are precisely aligned in a longitudinal direction using automated tensioning and positioning systems. Maintaining correct spacing is crucial to distributing load evenly and ensuring belt balance.
Rubber Embedding: A specially formulated rubber compound is applied to encapsulate the steel cords. This rubber serves both as a protective layer and a medium for adhesion between cords and belt covers.
Cover Application: Top and bottom rubber covers are pressed onto the corded core using a calendaring process. These covers may vary in thickness and hardness depending on the operational environment.
Curing and Vulcanization: The assembled belt is then vulcanized under heat and pressure in large presses. This stage bonds the materials together and enhances the belt’s resistance to wear, fatigue, and deformation.
In various industrial applications, performance differences between steel cord and fabric conveyor belts become evident. While fabric belts may offer better flexibility in short-distance applications, steel cord belts are generally preferred where low elongation and consistent tension control are needed.
Steel cord belts perform steadily in high-capacity systems and small downtime due to fewer joint failures and longer service intervals. Their ability to handle higher mechanical stress makes them more efficient in reducing spillage and misalignment over extended operations.
Another important aspect of steel cord conveyor belts is their ability to operate under diverse environmental conditions.
Temperature Resistance: Depending on the rubber formulation, these belts can function in environments involving elevated or reduced temperatures, such as foundries or refrigerated warehouses.
Moisture and Chemical Exposure: Protective rubber layers shield the steel cords from water ingress and chemical exposure. In environments where moisture or acidic conditions are present, additional rubber sealing or edge protection can be applied.
Underground and Tunnel Use: In confined environments, steel cord belts are favored for their fire-retardant and anti-static properties, which are essential for regulatory compliance and operational safety.
With increasing awareness of environmental impact, the recyclability and energy efficiency of steel cord belts have become relevant factors. Many belts are now produced using lower-emission manufacturing techniques, and components such as steel cords can be separated and repurposed after the belt's service life ends.
The steel cord conveyor belt represents a specialized solution that balances structural precision, environmental durability, and performance efficiency. Its manufacturing process supports customization for various industries, while its adaptability makes it a dependable choice for applications where operational stability and safety are priorities. Understanding these aspects allows users to make informed decisions tailored to specific project needs.