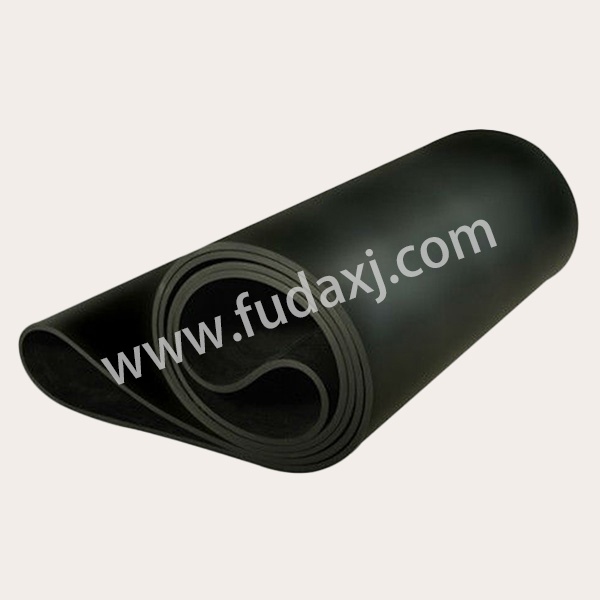
Rubber products (such as sealing products) are used under compression, and their compression resistance is one of the main properties that affect the quality of the product. The compression resistance of rubber is generally constant by compression set.
When the rubber is in a compressed state, physical and chemical changes will inevitably occur. When the compression force disappears, these changes prevent the rubber from returning to its original state, and compression permanent deformation occurs. The size of the compression set depends on the temperature and time in the compressed state and the temperature and time when the height is restored.
The size of compression set is one of the important indexes to measure the sealing performance and shock absorption performance of rubber products and the length of service life.
The study of various factors affecting the compression and permanent deformation of vulcanized rubber is of great significance to the production and testing of rubber sealing products and shock-absorbing products.
The influencing factors that affect the compression set of vulcanized rubber are:
1. Factors of rubber formula
Varieties of raw rubber; Varieties and dosage of additives
Both affect the cross-link density, which in turn affects the compression set.
Accordingly, we should pay attention to:
1. The structure of cross-linked bonds, polysulfide bonds are easy to decompose and have poor heat resistance, and high-sulfur and low-promoting systems should be avoided as much as possible. Single sulfur bond, high decomposition temperature, good heat resistance, so when sulfur vulcanization, it is necessary to use low sulfur and high promotion system as much as possible. The carbon-carbon bond has a higher decomposition temperature and the best heat resistance, so the DCP-S system is the best.
2. Density of cross-linking bond. The density of cross-linking is high, and the permanent deformation is small. Since permanent deformation is caused by viscous flow between molecular chains, cross-linked bonds can avoid relative slippage between molecules and reduce permanent deformation.
When designing the formula, the amount of the vulcanization system can be appropriately increased to increase the cross-linking density, and the increase in the amount of ZnO + stearic acid will also appropriately increase the cross-linking density. The use of peroxide vulcanization is to add a cross-linking aid will also be very helpful.