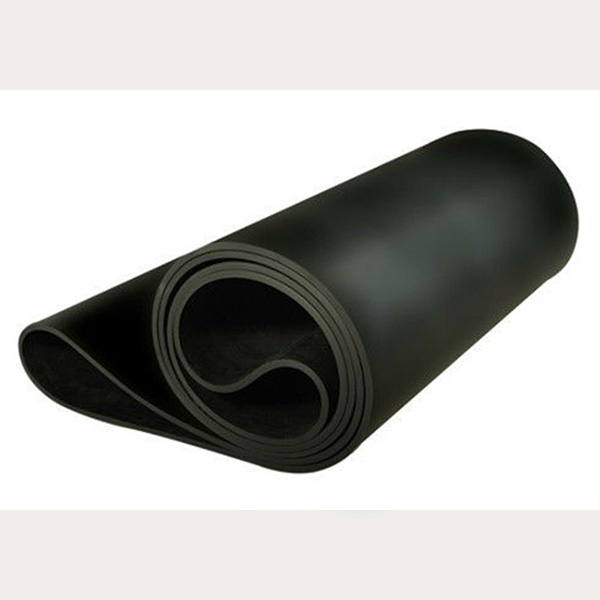
Choosing the right conveyor belt for a specific application involves considering several factors. Here are some steps to guide you through the process:
Identify the Application Requirements: Start by understanding the specific needs of your application. Consider factors such as the type of material being conveyed, its size and weight, the conveyor speed, the environment (temperature, humidity, chemicals), the desired throughput, and any special requirements or constraints.
Material Compatibility: Determine the compatibility of the conveyor belt material with the product being conveyed. Some materials may be abrasive, oily, corrosive, or have specific temperature requirements. Ensure that the belt material can withstand these conditions without degradation or contamination.
Belt Type: Select the appropriate belt type based on the application. Common belt types include flat belts, modular belts, timing belts, PVC belts, rubber belts, wire mesh belts, and others. Each type has its strengths and limitations, so choose the one that best suits your application requirements.
Belt Strength and Durability: Consider the load capacity and durability required for your application. The belt should be able to handle the weight of the conveyed material without stretching, sagging, or breaking. Additionally, assess the expected wear and tear based on the application's intensity and lifespan requirements.
Belt Width and Length: Determine the required belt width and length based on the dimensions of the product being conveyed and the space available. Ensure that the belt width is sufficient to support the material without spillage or excessive product contact.
Surface and Profile: Consider the surface characteristics of the belt. Depending on the application, you may require a smooth surface, grip-enhancing texture, or specific profiles such as cleats or corrugations for inclined or steep conveyance.
Operating Conditions: Evaluate the operating environment, including temperature extremes, moisture levels, and exposure to chemicals or oils. Select a conveyor belt that can withstand these conditions without significant degradation or reduced performance.
Maintenance and Cleanability: Consider the ease of maintenance and cleanability of the conveyor belt. Some applications may require frequent cleaning, while others may involve occasional maintenance. Choose a belt that facilitates easy cleaning and maintenance to ensure optimal performance.
Product
(1) Low density and high filling property
EPDM rubber is a kind of rubber with low density and its density is 0.87. In addition, it can be filled with oil and fillers which can reduce the cost of rubber products . Moreover, for the high Mooney value EPDM rubber, the physical and mechanical energy after high filling will not decrease significantly.
(2) Aging resistance
EPDM has excellent weather resistance, ozone resistance, heat resistance, acid and alkali resistance, water vapor resistance, color stability, electrical properties, oil filling and room temperature fluidity. The working temperature can be increased by adding suitable antioxidant. EPDM crosslinked with peroxide can be used under harsh conditions. When the concentration of ozone was 50 PPHM and the tensile strength was 30%, the EPDM rubber could not crack for more than 150 hours.